In a global stage characterised by the offshoring of manufacturing and the increasing complexity of the supply chain, industrial automation is emerging as a key enabler of efficiency and competitiveness. This article will explore five automation models that are redefining industry, addressing current challenges and paving the way for a more efficient and sustainable future.
1. Onshoring of manufacturing
In recent years, there have been shortages of both toilet paper and semiconductor chips.
These shortages affect manufacturers in a wide range of industries, from automotive to consumer electronics.
Most of the semiconductors used globally are produced in various regions.
Increased demand, supply chain challenges and raw material shortages have led to a growth in the number of manufacturers looking to relocate their operations.
Automation will be more in demand as a result of offshoring because manufacturers will need to add more automated procedures to compete with low-cost labor markets and offset employee shortages.
According to one article, robot sales hit a record high in 2021 as more manufacturers looked at increasing production with robots.
Between January and November, 29,000 robots worth $1.48 billion were ordered, up 37% from the same period in 2020.
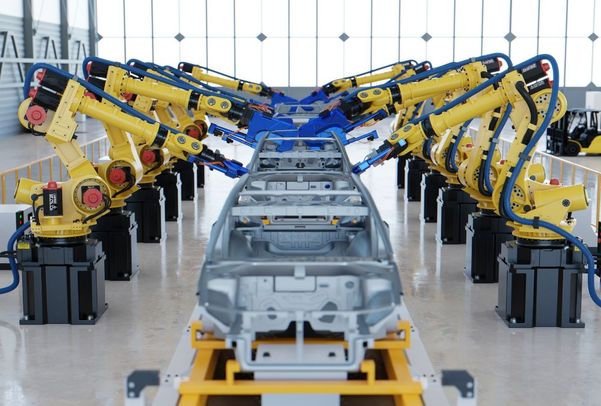
2. Intensified focus on cyber security
News of ransomware attacks against U.S. utilities has drawn attention to the need for improved cybersecurity.
A group of Russian hackers broke into Colonial Pipeline through the VPN network that employees used to access their systems remotely.
Bitcoin was used to pay the ransom, and since then, the hackers have become even bolder and continue to target manufacturing facilities, infrastructure and even individual consumers.
To safeguard their operations and assets, companies must now more than ever establish a highly effective and flexible cybersecurity strategy.
3. Conventional versus additive manufacturing
The use of 3D printing has recently taken the world by storm.
Since the 1940s, when the idea of 3D printing first emerged, the technology has advanced considerably thanks to improvements in tooling and filaments.
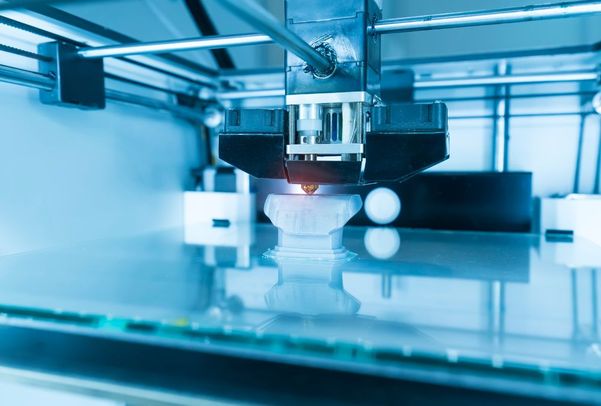
Today, 3D printing is used in additive manufacturing to produce industrial prototypes faster and more accurately.
Companies need to consider what ratio of traditional to additive manufacturing makes sense and how quickly they need to implement the new technology as the range of printable materials on all substrates expands.
In less than two years, hearing aid manufacturers switched from conventional to additive manufacturing, boosting manufacturing flexibility and enabling greater customization.
4. Relevance of predictive maintenance
Although predictive maintenance has been around for a long time, the need to collect data from each stage of the industrial manufacturing process has greatly increased in recent years.
The path of a manufactured product is examined at each stage. Sensors track vibrations, temperatures, noise, humidity and other factors to ensure that a line is running as efficiently as possible and to reduce waste and losses.
When a motor or bearing nears the end of its life cycle, condition monitoring systems alert the user.
The days of sending a technician to the plant to perform normal planned maintenance on an engine just because the schedule said it should be done are long gone.
Now we can accurately predict when that same engine will fail and when we should place a replacement order thanks to the ability to monitor all aspects of its performance.
As a result, there will be fewer instances of line stoppages or production reductions, reducing the impact on plant performance.
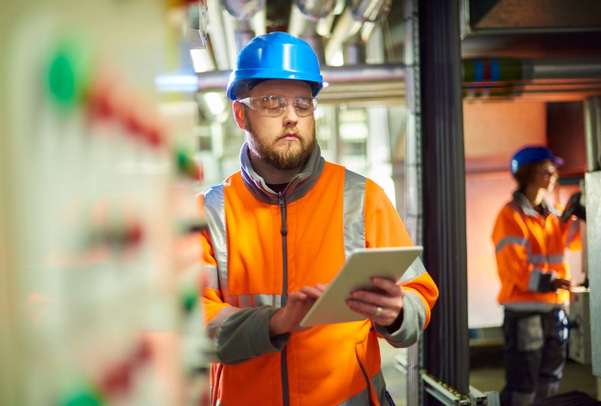
5. Eco-friendly and socially conscious business practices
Manufacturers are much more concerned about the environment today than they were ten years ago.
Consumer buying patterns have had a lot to do with it.
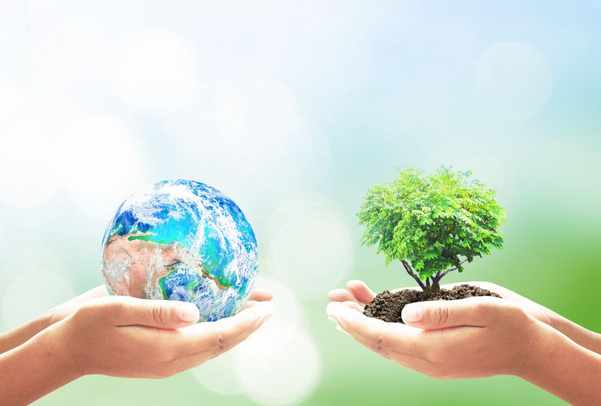
Today's consumers are much more likely to buy products from reputable manufacturers that take their environmental responsibilities seriously and use sustainable materials in their production.
The rising cost of energy and resources is pushing manufacturers to adopt more environmentally friendly processes, which will continue this trend.
Manufacturers contribute to minimizing adverse environmental effects by taking a holistic life-cycle view of the entire manufacturing process, the product itself, and the resources and raw materials.
Conclusion
Together, these automation models not only address immediate challenges, but also set a path towards a more efficient, safe and environmentally friendly industry. Industrial transformation, fuelled by automation and innovation, defines the future of manufacturing.
Five patterns in industrial automation